The dying craft of dyeing cloth
Traditional indigo textiles are making a comeback after falling out of public favor in the 1980s
One of the first things that catches the eye upon entering Wuzhen from its Xiazha entrance are the long pieces of indigo textiles with white patterns that gently sway from tall poles.
Called lan yin hua bu, or "blue floral print cloth", these creations are the product of a traditional craft that has been around for thousands of years.
According to Xun Zi, a book on Confucianism, Chinese had as early as the 3rd century BC been extracting indigo dye from plants, but it was only around the Song Dynasty (960-1279) when this dye was widely used for textiles.
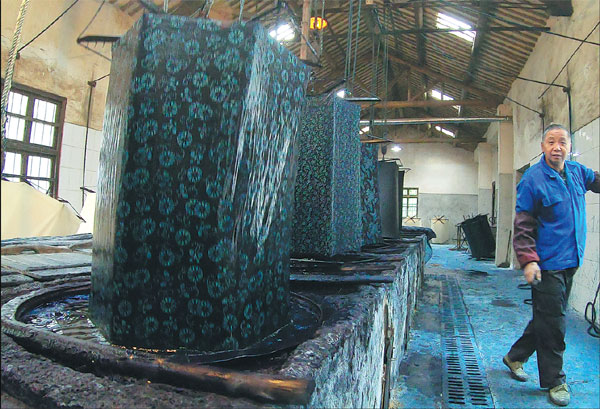
Such textiles were widely used in society up until the late 1980s when its popularity started to decline because machines could quickly manufacture synthetic dyes that came in different colors. Consumers were now spoilt for choice. Indigo just didn't seem very exciting anymore.
"During my childhood in the 1960s, clothes, tablecloth and curtains were all made by this textile," recalled Zhou Jiming, who runs Tongxiang Indigo Print Making, one of the oldest workshops for such cloth in the city.
"During the peak of this craft in the mid-1980s, our company had about 130 workers and our products were exported to places like Japan. Today, we only have around 20 workers."
Zhou was 28 when he first learned how to do indigo dyeing at a workshop that was located along the route to his school. He later joined Tongxiang Indigo Print Making and has since been working there for the past 32 years.
Today, his workshop is able to create about 200 patterns, many of which are derived from Chinese folklore. He can also create customized designs.
The most popular patterns are those featuring flowers and animals as they are often symbolic in Chinese culture. For example, the peony is a symbol of wealth and prosperity, while pine trees represent longevity.
Those unfamiliar with this craft may think that this textile is made simply by imprinting white patterns on blue cloth. However, the production process, which is almost completely manual, is a lot more complicated than that.
The first step of the process involves carving out the motifs on a thick paper template by hand. Zhou said that an intricate design would take a skilled carver up to four days to complete.
These patterns are then transferred onto white cotton cloth by brushing a dye-resistant paste made with lime and grounded soy bean over the template. It takes about three days for this paste to dry, following which the cloth undergoes the dyeing process.
Indigo dye is extracted from the woad plant, also sometimes known as Asp of Jerusalem, by grinding and fermenting its leaves. The dye is then poured into a large caldron where the cloth is immersed a number of times until it turns indigo. Following this, workers extend the cloth and scratch off the dye-resistant paste, leaving behind the white motifs underneath.
The last step of the process is the washing of the cloth to remove any remnant particles and hanging it out to dry on poles.
In 2006, this traditional craft was listed as a national intangible heritage. Two years later, Zhou was named as one of the inheritors of this craft.
Though such textiles are no longer as popular as before, Zhou's workshop still sells about 2 million yuan ($303,000) worth of it every year, but most of his clients today are souvenir stalls and clothing boutiques catering to tourists.
"People used to consider these sort of clothes very special. Today, such textiles are more for people who appreciate old culture," said the 66-year-old.
When asked why he has not packed up the business to pursue something more lucrative, Zhou said that he has a responsibility to teach what he knows to the next generation and ensure this traditional craft does not go extinct.
He revealed that he has plans to build a museum to showcase this traditional handicraft and teach people how to create their own indigo cloth.
"Allowing people to experience the process of making this textile is an essential element in the preservation of this craft. It helps them to appreciate the effort that goes into making such products," he said.
"Today, there are many machine-made alternatives in the market that use synthetic dye, but they cannot be called lan yin hua bu. This product we have here is all-natural. There's hardly anything else like it." he added.
xingyi@chinadaily.com.cn
Zhou Jiming's Tongxiang Indigo Print Making is one of the oldest workshops for blue floral print cloth in Tongxiang, Zhejiang province. Photos by Gao Erqiang / China Daily |
(China Daily 12/03/2017 page10)